DRILL
BAR
Drill bar or micropile is a deep foundation solution capable of withstanding substantial structural loads. These elements, typically ranging from 100mm to 350mm in diameter, offer exceptional performance and versatility in a wide range of construction scenarios.
With the ability to extend to depths of up to 50 meters, drill bar or micropiles provide a robust and reliable means of transferring structural loads into the ground, ensuring the stability and integrity of the entire structure.
WHAT THEY’RE USED FOR
The drill bar system stands as a versatile solution for various construction challenges, particularly in scenarios with restricted access or proximity to existing structures. This system offers flexibility and performance, making it well-suited for a wide range of ground conditions, including rocky terrain. As such, drill bar systems find widespread application across diverse sectors, including commercial, infrastructure, and rail projects.
One of the key advantages of drill bar systems is their ability to address a multitude of construction needs and challenges. Whether it's stabilising unstable ground, minimising settlements, reinforcing existing foundations, or providing structural support for tunnels, basements, highways, and bridges, this system excels in delivering reliable and efficient solutions. By effectively transferring loads into the ground, drill bar systems enhance the stability and longevity of structures, ensuring their safety and integrity over time.
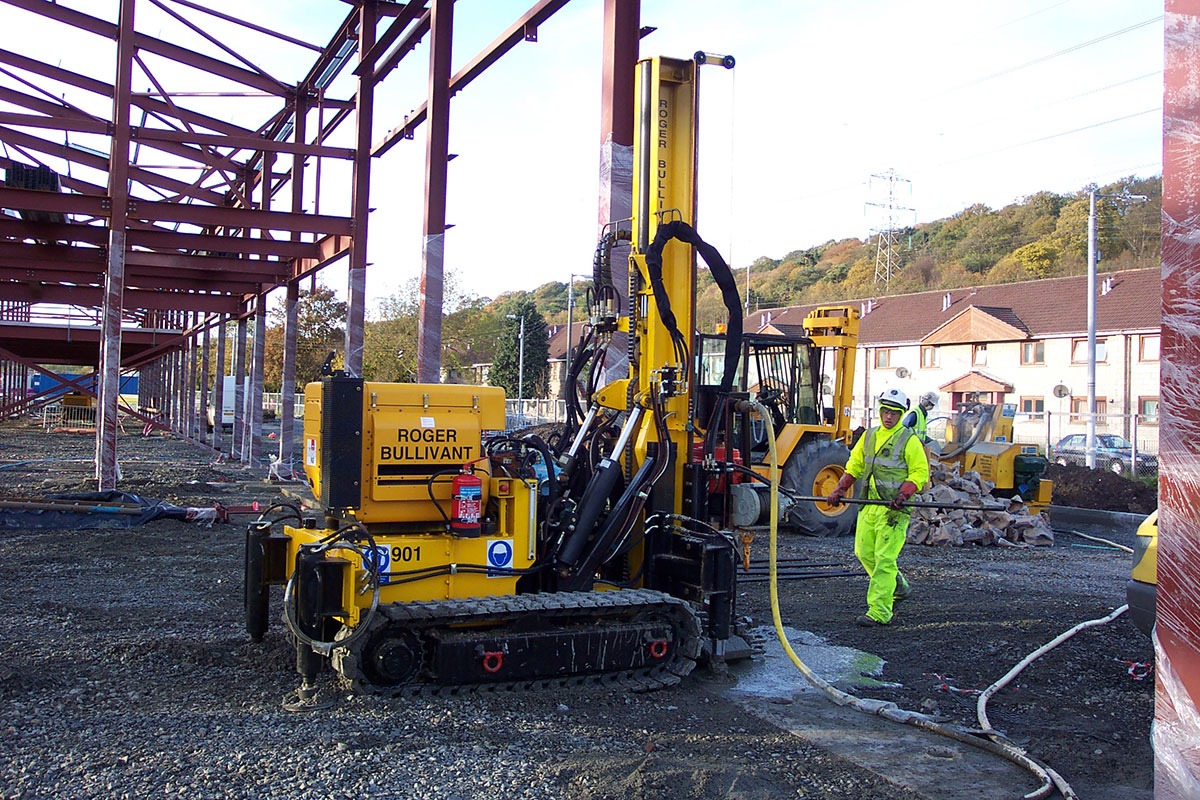
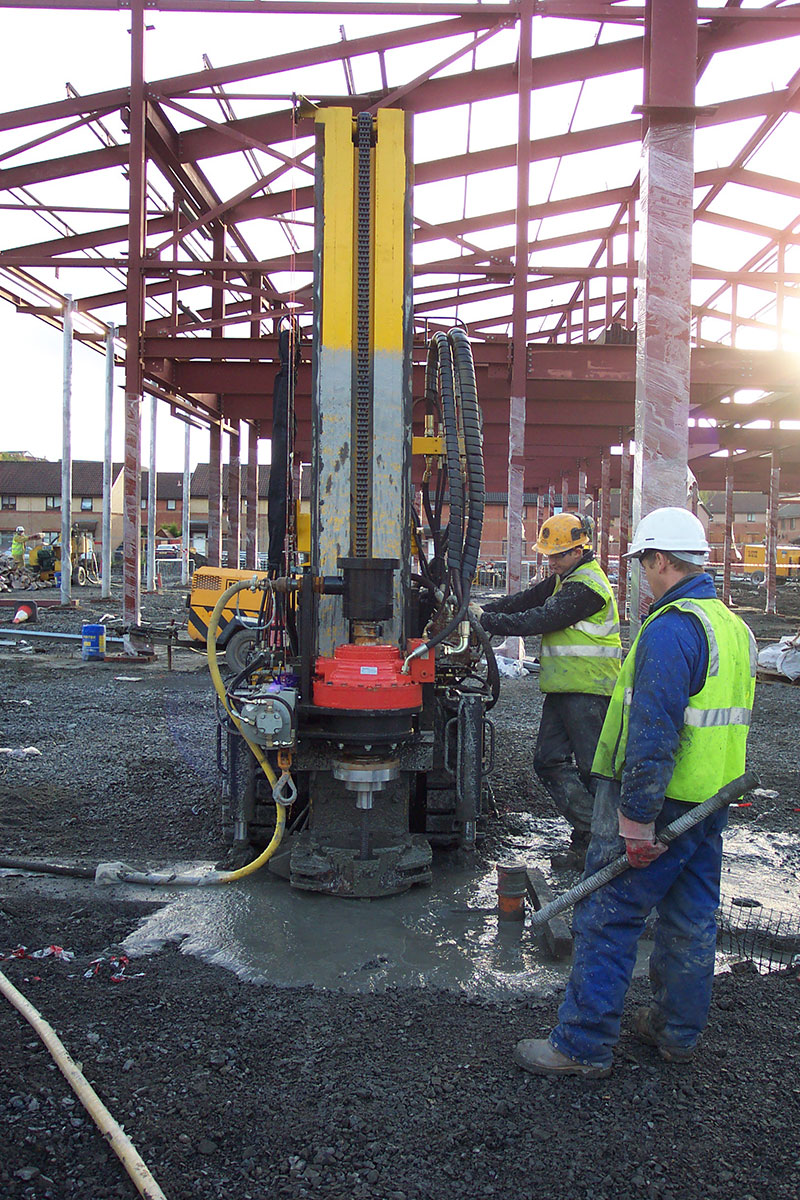
THE PROCESS
Micro piles are a foundation solution characterised by their hollow bar construction, enabling simultaneous drilling and grouting operations. The hollow bars typically range in diameter from 40/20mm to 103/43mm, with a central hole that facilitates the boring process and injection of grout during installation.
The installation process begins with the insertion of the hollow bar micropile into the ground using a specialised drill rig equipped with an appropriate drill bit to suit the underlying ground conditions. The drill bit is threaded to the first section of the hollow bar, allowing for efficient penetration into the soil or rock formation. As the micropile is advanced into the ground, additional hollow bars are threaded and drilled to depth using the rotary percussive hammer on the drill rig via a swivel flushing head. This innovative setup enables simultaneous drilling and grout flushing, streamlining the installation process and maximising efficiency.
The installation procedure uses a weak flushing grout to stabilise the annulus, consequently eliminating the use of full-depth casings. Once the micropile has reached design depth full-strength grout is flushed through the hollow stem of the micropile, to create an OPC grout body with the profiled surface of the grout body transferring the loads into the surrounding ground. This grouting process serves multiple purposes, including enhancing the structural integrity of the pile, improving load-bearing capacity, and providing corrosion protection for the reinforcement bar.
WHY USE Drill Bar?
- The system is fast, simple and flexible
- Can be installed in any type of ground condition, particularly unstable soils
- Unaffected by changing soil conditions
- Perfect for structural repairs and underpinning
- Easily installed in confined spaces and limited access
- Ability to accommodate high load conditions
- Minimal vibrations and noise pollution
- Minimum site preparation
- Installed by RB in-house small and lightweight mini piling equipment
- Does not require temporary casing
ROGER BULLIVANT
QUALITY CONTROL
We successfully deliver projects to the highest standard, safely, on time, within budget, and with care for the environment and communities. Clients choose RB time and time again thanks to our proven track record.
All products are manufactured to BSEN, ISO, and CE accreditation. We are committed to ensuring we continuously deliver high quality, robust service, and product to our clients. At RB we continuously review and access where we can further improve.
We are proud to be recognised and awarded the RoSPA gold award for the sixth year running for the exceptionally high standards towards the health and safety of our employees.