Roger Bullivant Limited (RBL) stands as a frontrunner in the industry, renowned for its expertise in designing, manufacturing, and installing Precast Segmental Piles. Our comprehensive piling solutions, RBL offers Precast Caps—a specialised flared head component designed to enhance the efficiency and versatility of foundation systems.
Our package solution encompasses the entire process from start to finish, including design, manufacturing, setting out, cropping, and installation. This comprehensive approach ensures seamless integration and coordination across all stages of the project, minimising potential delays and streamlining project execution.
WHAT THEY’RE USED FOR
Roger Bullivant Limited's Precast Cap solution offers unparalleled versatility, making it an ideal choice for a wide range of commercial projects. Primarily designed to support internal concrete slabs, Precast Caps are particularly well-suited for applications in structures such as sheds, warehouses, and industrial facilities. Their robust construction and flared head design ensure reliable load distribution, providing stable support for heavy-duty flooring systems commonly found in commercial environments.
In addition to their primary function, Precast Caps can also serve as an internal piled slab replacement. By incorporating Precast Caps into the foundation design, the need for traditional insitu piled slabs can be eliminated, resulting in streamlined construction processes and cost savings. This innovative approach not only enhances construction efficiency but also offers greater flexibility in design and layout optimisation.
Furthermore, Precast Caps are suitable for use as external concrete hardstanding, providing durable and stable surfaces for outdoor areas such as parking lots, loading docks, and storage yards. Their versatility extends to various environmental conditions, making them a reliable choice for both indoor and outdoor applications.
Overall, Roger Bullivant Limited's Precast Cap solution offers a comprehensive foundation solution for commercial projects, combining durability, versatility, and cost-effectiveness to meet the diverse needs of modern construction environments.
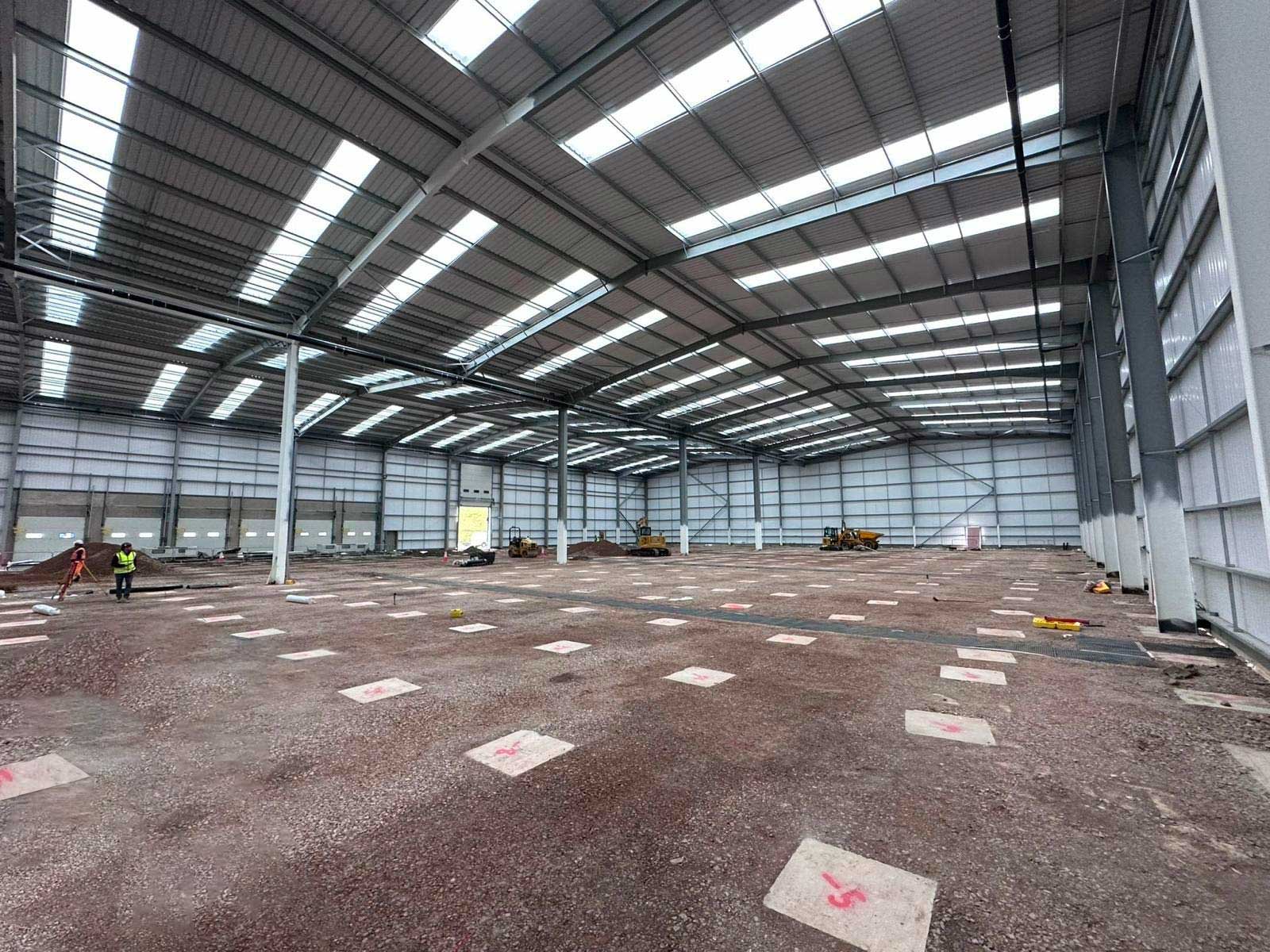
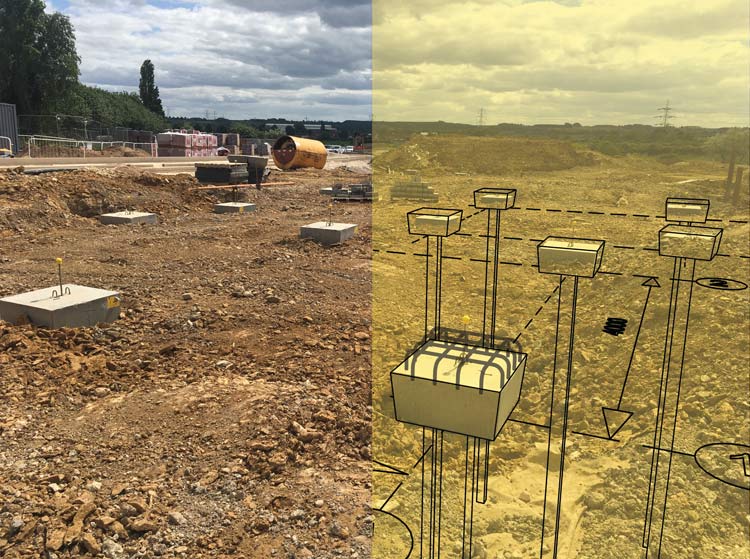
THE PROCESS
Following the installation of precast piles, a process ensues to ensure the structural integrity and alignment of the foundation system. Initially, RBL excavates the area surrounding each pile to prepare for the subsequent steps.
Next, the Driven Precast Concrete Piles are mechanically cropped to the desired cut-off level, ensuring uniformity and consistency across all piles. Additionally, the central bar within each pile is trimmed to the appropriate length, ensuring it does not protrude above the pile cap level.
With the piles prepared, the precast cap is lowered onto each pile, seated on an even grout bed. This process guarantees a final level tolerance of +0/-10mm, ensuring precise alignment and stability.
Following the installation of the precast caps, RBL or the assigned groundworker utilises the excavated material to backfill the surrounding area around each pile. This backfilling process is conducted, compacting the material in layers using a small vibrating wacker plate. This ensures optimal compaction and stability of the backfilled soil, creating a solid foundation ready to receive further construction elements.
This process not only ensures the structural integrity and alignment of the foundation system but also maximises efficiency and minimises waste.
WHY USE Precast Caps?
- Reduces on site activities once the precast pile is cropped, shuttered and concrete cap is placed
- Package includes design, manufacture, setting out, cropping and installation.
- Factory quality products utilising low carbon concrete
- Non-weather dependant
- Reduced site waste and wash out
- Various precast pile cap sizes depending on load requirements.
- Reduces the depth of insitu concrete slab, providing savings to the project
- Takes the operation off critical path and can be installed once structure sides and roof on.
EXAMPLE PROJECTS
ROGER BULLIVANT
QUALITY CONTROL
We successfully deliver projects to the highest standard, safely, on time, within budget, and with care for the environment and communities. Clients choose RB time and time again thanks to our proven track record.
All products are manufactured to BSEN, ISO, and CE accreditation. We are committed to ensuring we continuously deliver high quality, robust service, and product to our clients. At RB we continuously review and access where we can further improve.
We are proud to be recognised and awarded the RoSPA gold award for the sixth year running for the exceptionally high standards towards the health and safety of our employees.