At Roger Bullivant Limited, we take pride in offering an innovative, efficient, and sustainable foundation solution, with our RBeam Precast Ground Beam Foundation System being a leader in the industry. This system isn’t just a foundation solution; it’s a foundation solution that redefines how they are designed, manufactured, and installed. Classified within Category 3 Modern Methods of Construction (MMC), this system follows an industrialised approach that outperforms traditional methods as outlined in the diagram below. Let’s take you behind the scenes on how the RBeam system works…
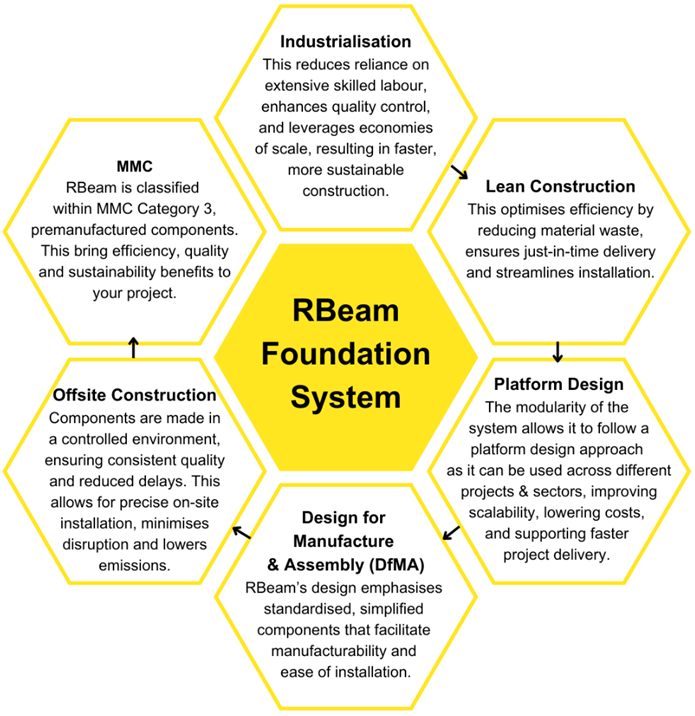
Step 1: High-Quality Concrete – Built to Last
The RBeam system is manufactured using low-carbon concrete, designed for sustainability and strength. This specialist concrete mix reduces the carbon footprint without compromising on durability or strength. Our concrete is designed and specified to ensure enhanced performance that is suitable under different conditions, making it robust and durable enough for a variety of soil types allowing the beams to perform in demanding environments. The concrete mix is fine-tuned to resist cracking and shrinkage during our manufacturing process, ensuring consistent quality, strength, and the flexibility to meet the demands of our clients. The use of high-quality concrete with efficient reinforcement allows the RBeam System to be suitable for a multitude of building and structure types including low rise residential and commercial buildings.
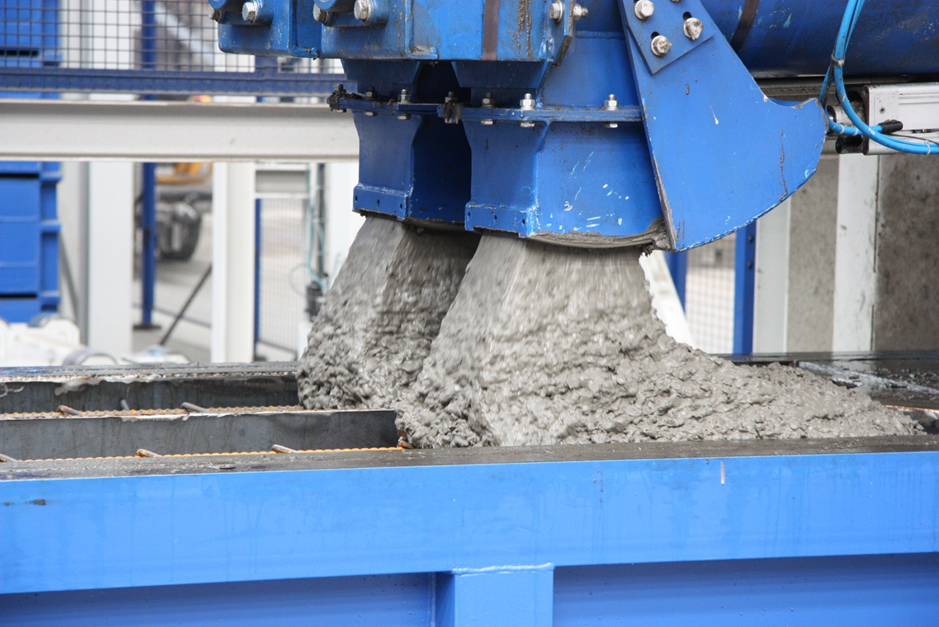
Step 2: Precision Formation – Manufactured in a Controlled Environment
All RBeam precast beams are manufactured offsite at our manufacturing facility in South Derbyshire. This controlled environment ensures the beams are produced with precision and consistency, free from the unpredictable variables of on-site concrete pouring.
From the concrete mix being prepared using our on-site concrete batching plant to reinforcement being fabricated using our own rebar fabrication welding and bending plant. The beams are cast using steel moulds within one of our two purpose built automated concrete production plants that are supported with long-bed production moulds. The casting process ensures uniformity and precision, so each beam is dimensionally accurate and adheres to strict quality standards every time. The use of steel moulds with our concrete mix enhances a smooth finish of each beam making them ideal for projects where they are visible above ground.
The manufacturing process allows us to produce foundation beams in various dimensions, depending on project needs. Beams are typically 400mm wide, but we can also manufacture widths of 450mm and 600mm to meet specific project requirements. Beams are available in three depth options: 300mm, 375mm, and 450mm, with the length of the beams ranging from 900mm to 6000mm, manufactured in 150mm increments. This range of standardised beams allows for flexibility in design to tailor a foundation solution that does not compromise on the requirements of the project, and speed of installation as result of having a stockyard of our RBeams stacked ready to be delivered to site ensures reliable project programme delivery.
This quality-controlled environment ensures our RBeams are produced with precision and consistency, free from the unpredictable variables of on-site concrete pouring.
RBeam is manufactured using either the semi-automated Quadra Optimal 6000 machine or through more traditional methods with linear moulds. The Optimal machine operates with a set of fixed moulds selected based on historical demand. The casting process follows a 24-hour cycle, starting with the demoulding of the previous cast. After demoulding, the mould is cleaned, oiled, and prepared with the appropriate reinforcement cage before concrete is poured via an automated delivery system. The mould is then placed in the curing area until the next day, when it is turned over to release the product, beginning the process again.
Linear moulds offer flexibility, allowing us to quickly respond to short-term demand spikes. These moulds feature moveable steel shutters, enabling the production of beams of varying lengths in the same mould. We have the capacity to produce up to 4,500 metres of beams per week across the range.
Beams are transported to our stockyard using multi-directional electric forklifts, where they are stacked for curing. Thanks to their stackable design, we can store up to 10,000 metres of beams at any given time. Stacks are arranged on a first-in, first-out basis to ensure that products are dispatched only after the concrete has reached its designed strength, verified by our in-house concrete testing facility.
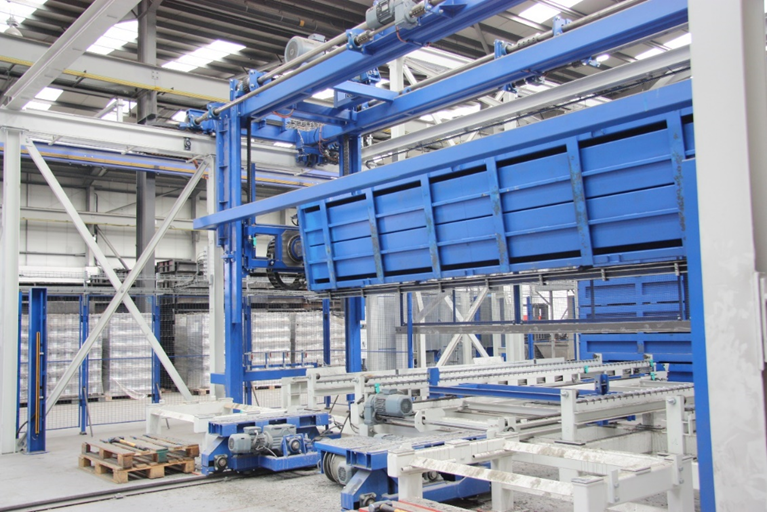
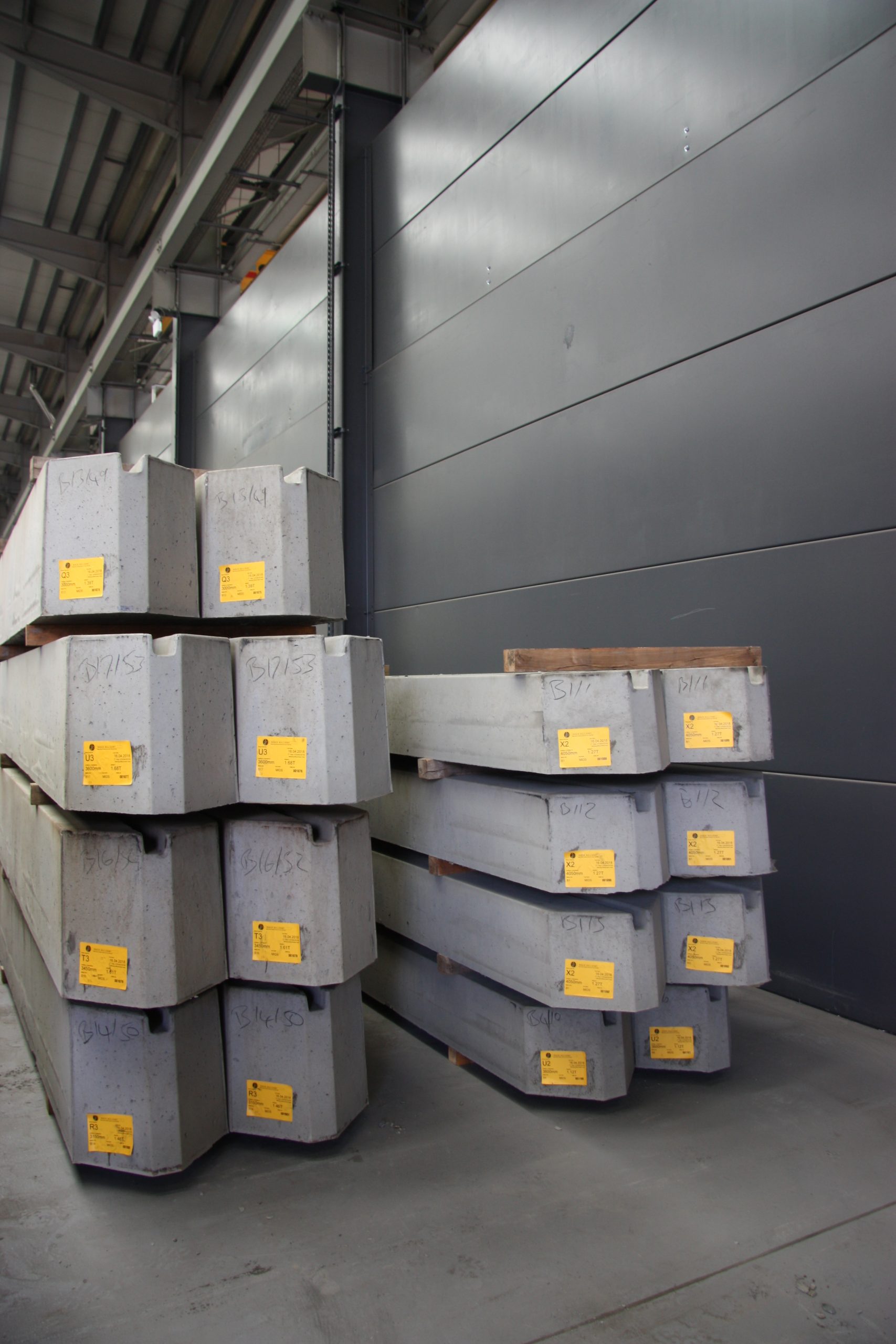
Step 3: Efficient Installation – Tailored for Your Project
Individual installation teams can install several hundred metres of beam per week, significantly accelerating project timelines. Since the beams are manufactured offsite, they can be delivered on a ‘just in time’ basis and immediately installed, with no waiting for curing time like traditional cast foundations. The reduced need for excavation and material movement means a safer and more streamlined construction process.
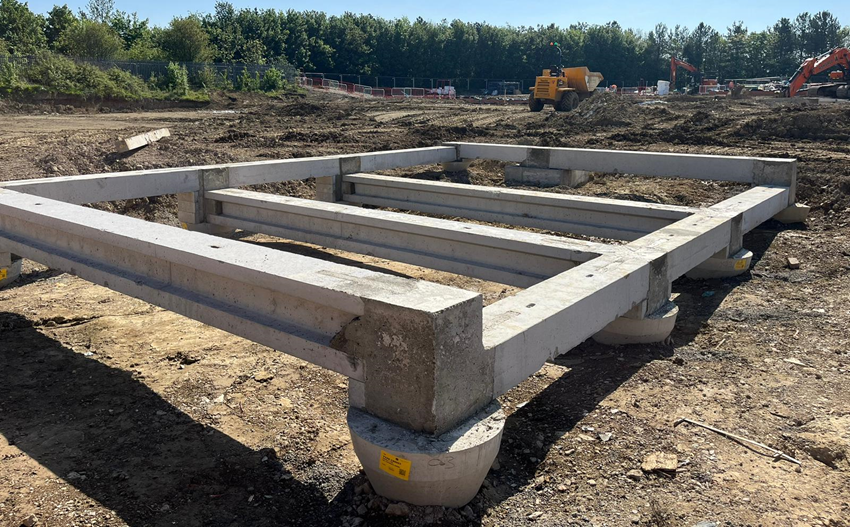
Why Is the RBeam System Better?
Here’s why RBeam outperforms traditional foundation methods:
1. Speed and Efficiency
With RBeam, speed is a major advantage. Traditional methods, such as trench-fill foundations, require significant excavation, curing time, and multiple stages of on-site work. In contrast, RBeam is pre-manufactured and can be installed quickly, saving both time and labour. This results in a faster overall build time, allowing construction teams to move swiftly from foundations to the rest of the structure.
2. Sustainability and Reduced Waste
The RBeam system focuses on environmental responsibility. The use of low-carbon concrete and minimised on-site waste makes it a green alternative to traditional methods. The “kit of parts” approach means fewer materials are needed and less gets wasted during construction. All RBeam designs are optimised though selection of fit for purpose solutions from our range of standardised manufactured foundation beams and components that form part of the RBeam system. This ensures efficient cost-effective use materials specified without compromising on project specific requirements.
3. Less Excavation and Safer Construction
By minimising excavation, the RBeam system reduces the overall footprint of foundation work. This makes it ideal for projects where space is limited on site, or where ground conditions are challenging. Moreover, the reduced need for deep trenching improves on-site safety, making the installation process safer for site installation teams.
4. Adaptable to Different Soil Conditions
RBeam is designed to perform in a variety of ground conditions, even on sites with heave potential. This adaptability is a major improvement over traditional methods that would require complex solutions to challenging soils and sites.
5. In-House Manufacturing and Stock Holding
Because we design and manufacture a unique standard length precast system in-house, we can maintain a large stock of piles, caps, and beams. This results in reduced lead times and faster project commencement, eliminating the reliance on external suppliers or delays due to production timelines. Our facility’s capacity to produce over 220,000 metres of precast foundation beam per year ensures we can meet demand for any project scale.
From its sustainable low-carbon concrete mix and precision manufacturing process to its rapid on-site installation that minimises excavation and material waste. RBeam is engineered to improve project outcomes offering a faster, greener, and more cost-effective solution that adapts to even the most challenging ground conditions and sites — delivering a better, smarter, and faster solution.
Let us help you bring these benefits to your next project! Contact us at Roger Bullivant Limited today to see how RBeam can work for you.